Vacuum Pump Troubleshooting
When your industrial vacuum pump goes down, it can cause significant problems for your company. In addition to the financial costs associated with downtime, you may also experience production delays, quality control issues, and other problems.
It’s important to keep your vacuum pumps in top-quality shape and do proper maintenance on your system components to try to avoid these issues. However, when they happen, it is so important to have quality vacuum pump troubleshooting skills. other problems.
That is why it is so important to have quality vacuum pump troubleshooting skills. If you lose pump pressure or if your industrial vacuum pump goes down altogether, it can cause significant problems for your company. In addition to the financial costs associated with downtime, you may also experience production delays, quality control issues, and other problems associated with a faulty pump operation. Remember that you can get an immediate download of the Vacuum Pump Troubleshooting Guide on this page.
There are a few common problems that our customers experience with their liquid ring vacuum pumps. In the next sections, we will discuss some of these problems and how to do correct vacuum pump troubleshooting.
When it seems you are having issues with a vacuum pump, it may or may not be a mechanical failure with the vacuum pump itself. On many occasions, we can prevent costly and unnecessary repairs or replacements with our ability to diagnose the problem as something within the system such as the motor, water supply, leaks or blockages, etc.
If your vacuum pump is down, the first step is to check for power going to the unit. If the unit still isn’t receiving power, you may have blown fuse or a bad start capacitor. Once you have checked for power, and you find the unit is still not working, please give us a call and let us help troubleshoot the problem.
We have over 30 years of experience in the industry and can help you get your vacuum pump up and running again. There are a few common problems that our customers experience with their liquid ring vacuum pumps.
Please call us to help assist you with any of your troubleshooting needs.
(see below for further information)

SYMPTOM – NO VACUUM
Probable Causes
a) Pump not rotating
b) Pump rotating backward
c) Pump is running dry
d) Defective vacuum gauge
e) Isolation valve improperly opened or closed
Solutions
a) Check motor/starter
b) Reverse motor polarity
c) Feed sealant continuously
d) Replace gauge
e) Operate valves correctly
SYMPTOM – REDUCED PUMP CAPACITY OR INSUFFICIENT VACUUM
Probable Causes
a) Air leak in system
b) Low rotational speed
c) High sealant temperature
d) Low sealant flow rate
e) Inlet suction piping clogged or restricted
f) Undersized inlet piping
Solutions
a) Locate and repair
b) Check voltage, sheave sizes, belt tension, and gear speed
c) Adjust coolant flow and temperature
d) Increase flow
e) Clear inlet piping
f) Increase inlet pipe size
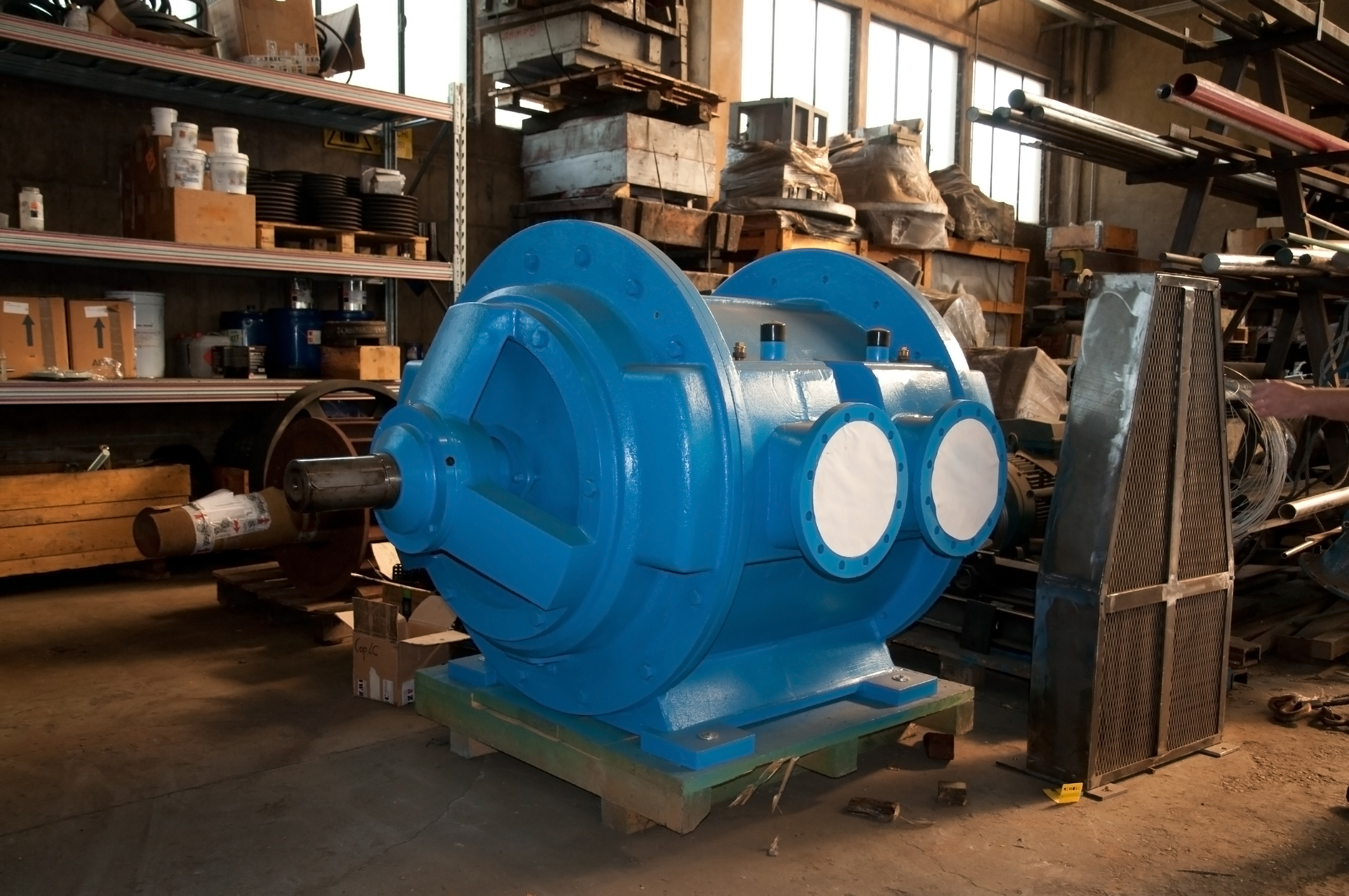
SYMPTOM – VACUUM LEVEL UNSTABLE; PUMP SURGING
Probable Causes
a) Pump operating below suggested minimum vacuum
b) High sealant flow rate
c) High flow or widely varying flow of process liquid through pump inlet
d) Inlet separator flooding
e) Low areas in inlet piping
Solutions
a) Review sysem requirements and pump performance curves
b) Decrease flow
c) Install inlet separator with barometric drop-leg or unloader pump
d) Check separator sizing, barometric drop-leg design, or condition of unloader pump
e) Locate and eliminate trapping liquid
SYMPTOM – MOTOR OVERLOADS OR DRAWS HIGH AMPERAGE
Probable Causes
a) High discharge pressure
b) High sealant flow rate
c) Rotational speed too high
d) Coupling sheave misaligned
e) Defective bearing
f) Pump binding
Solutions
a) Check discharge rate
b) Decrease flow
c) Check motor, drive components
d) Realign
e) Replace bearing
f) See “Pump binding”
SYMPTOM – EXCESSIVE NOISE OR VIBRATION
Probable Causes
a) Cavitation
b) High sealant flow rate
c) High discharge pressure
d) Coupling sheave misaligned
e) Defective Pump or motor
f) Pump not properly anchored
g) Poor structural foundation
Solutions
a) Seek to lower sealant temperature
b) Decrease flow
c) Check discharge rate
d) Realign
e) Replace bearing
f) Anchor properly
g) Repair, improve foundation
SYMPTOM – PUMP BINDING
Probable Causes
a) Build up of rust, scale
b) Foreign object in pump
c) Packing rings too tight
d) Clearances improperly set
Solutions
a) Clean pump interior – process solids on pump interior
b) Remove object
c) Adjust packing rings
d) Readjust clearances
SYMPTOM – PUMP OVERHEATING
Probable Causes
a) Low sealant flow rate
b) High sealant temperature
c) Defective bearing
d) Coupling sheave misaligned
e) Pump binding
Solutions
a) Review system requirements and pump performance curves
b) Decrease flow
c) Install inlet separator with barometric drop-leg or unloader pump
d) Check separator sizing, barometric drop-leg design, or condition of unloader pump
e) Locate and eliminate trapping liquid
SYMPTOM – ABNORMAL BEARING WEAR
Probable Causes
a) Inadequate/excessive lubricant
b) Contaminated lubricant
c) Coupling sheave misaligned
d) Excessive belt tension
e) Strain from piping
f) Soft foot on pump
g) High discharge pressure
h) High thrust load on out-board bearing
Solutions
a) Review and initiate correct lubrication procedures
b) Inspect/replace ceiling devices, flingers, and lubricate
c) Realign
d) Properly adjust belt tension
e) Support piping, use flexible connectors
f) Properly shim and anchor pump
g) Check discharge line
h) Split service pump with a vacuum differential greater than 5″HgV from one side of pump to other
The staff at Vacuum Pump Systems, Inc. can advise you regarding repairs, rebuilt systems, new pumps, and complete vacuum pump packages Let us help you with your pump needs including Vooner, Dekker, NES, and replacement pumps for the Nash* CL Series.